Rising PSF & VSF prices hurt Indian MSME spinners, CITI data reveals
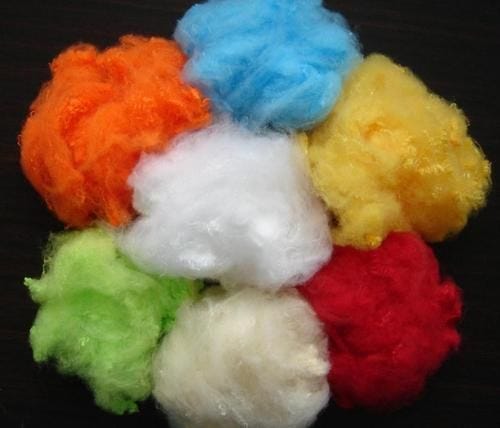
A recent report by CITI, authored by Manoj Sharma, a stark reality has emerged about Indian yarn manufacturers: a significant price gap between domestic and international prices of critical raw materials, Polyester Staple Fiber (PSF) and Viscose Staple Fiber (VSF). The findings, compiled for February 2025, underscore a potential threat to the competitiveness of Indian textiles in the global market.
Price disparity analysis
The report, titled 'Domestic and International Weekly Price Comparison of PSF and VSF for February 2025', delves into the cost dynamics affecting Indian manufacturers vis-à-vis their Chinese counterparts, utilizing data from China Chemical Fibre (CCF).
Key highlights
PSF price variance: Throughout February, the price difference between domestic PSF prices for Micro, Small, and Medium Enterprises (MSME) spinners and international prices (CCF) ranged from 14 per cent to as high as 35 per cent. This persistent gap indicates a substantial cost burden on Indian manufacturers compared to their international peers.
VSF price differential: Similarly, VSF prices showed a notable disparity, albeit slightly lower than PSF, ranging around 14-15 per cent higher domestically compared to international benchmarks.
Exchange rate impact: Fluctuations in the $/Rs exchange rate during February influenced the overall costs, albeit marginally. The exchange rate dynamics contributed to the variation in domestic prices when converted from international benchmarks.
Comparative analysis: January vs February 2025
Comparing data from January to February reveals a consistent pattern:
PSF: While the absolute price difference in Indian Rupees fluctuated slightly, the percentage difference remained consistently high. In January, the disparity ranged from 33.78 to 36.08 per cent, while February saw figures from 34.23 to 35.59 per cent. This persistence indicates a prolonged challenge for Indian PSF manufacturers.
VSF: The price difference in Rs decreased marginally in February compared to January. However, the percentage difference remained stable, indicating continued cost discrepancies in this segment as well.
Implications for industry
The higher domestic prices of raw materials highlighted in the CITI report could severely impact the profitability and global competitiveness of Indian yarn manufacturers. Importantly, the report clarifies that international prices do not reflect Indian landed costs, which include additional expenses like CIF, BCD, and other levies.
This the report serves as a crucial wake-up call for the Indian textile industry. Addressing the price disparity is imperative for sustaining growth and competitiveness. Potential strategies include optimizing input costs, enhancing operational efficiencies, and exploring policy interventions to mitigate the impact of high raw material costs.
Moving ahead, stakeholders, including manufacturers, policymakers, and industry associations, must collaborate to devise comprehensive strategies. These strategies should not only reduce the cost differentials but also foster an environment conducive to long-term sustainability and global competitiveness in the textile sector.