BASF opens world's first loopamid plant in China to boost recycled yarn production
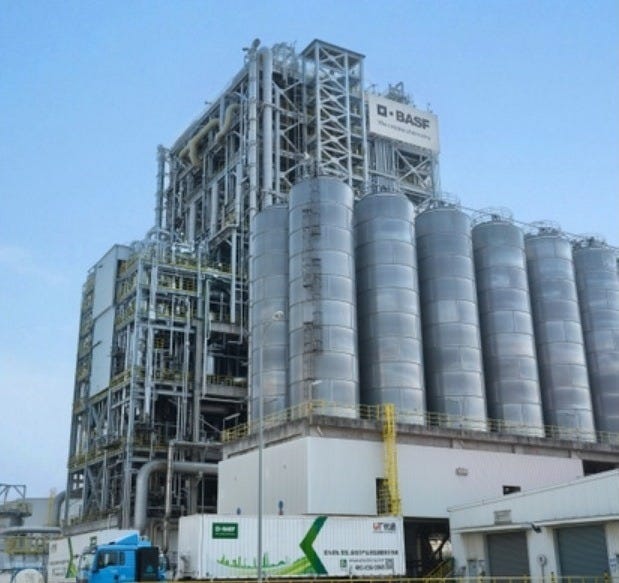
German chemical major BASF has launched the world’s first commercial-scale plant for loopamid, a fully recycled polyamide 6 made entirely from textile waste. Located in Shanghai, China, the facility has an annual capacity of 500 metric tons and is designed to support the growing demand for sustainable materials in the textile and yarn industry.
Loopamid enables textile-to-textile recycling of polyamide 6, even in complex fabric blends containing elastane. The recycled polymer is already being used by yarn manufacturers and meets the Global Recycled Standard (GRS) for environmental and social compliance. BASF emphasized that loopamid helps close the textile loop by transforming industrial textile waste such as offcuts and defective pieces into valuable raw material.
The company plans to gradually increase the share of post-consumer waste, including end-of-life garments, in its feedstock. However, challenges remain due to the need for sorting mixed fibers, removing accessories, and handling various dyes and additives. To overcome these barriers, BASF is actively collaborating with customers and partners to develop efficient waste collection and sorting systems.
This new facility marks a major step in advancing circularity in textiles and supporting the industry’s shift toward sustainable yarn and fiber solutions.